Comprehensive Guide to Injection Molding Tooling in Metal Fabrication
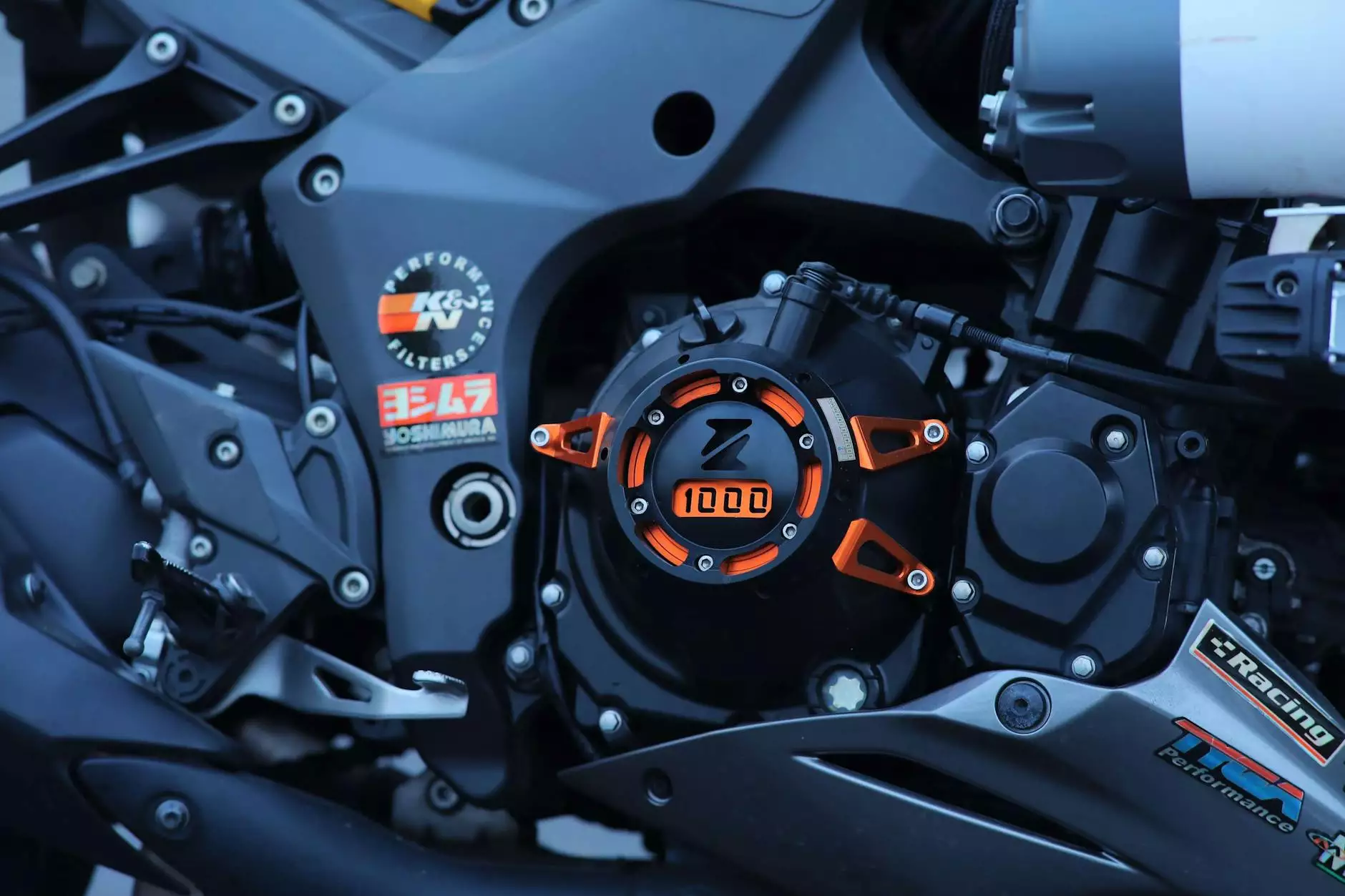
In the realm of manufacturing, injection molding tooling stands out as a critical component that significantly influences product quality and production efficiency. As the business landscape evolves, understanding the intricacies of this process is essential for companies aiming to excel in the competitive field of metal fabrication.
Understanding Injection Molding Tooling
Injection molding is a manufacturing process used to produce parts by injecting molten material into a mold. The tooling aspect refers to the custom tools and molds designed to create specific components. This process is widely utilized in industries ranging from automotive to consumer goods, making it a fundamental part of modern manufacturing.
The Process of Injection Molding Tooling
The injection molding process involves several steps:
- Design and Prototype: Initial designs are created, often using CAD software, and prototypes are made to ensure accuracy.
- Tooling Creation: A mold is fabricated based on the prototype, tailored to achieve the desired shapes and volumes.
- Injection: The molten material is injected into the mold at high pressure, filling every cavity to create a solid part once cooled.
- Cooling: After injection, the material is allowed to cool, solidifying in the mold.
- Demolding: The final part is extracted from the mold, ready for additional processing or finishing.
The Importance of Injection Molding Tooling in Business
Incorporating effective injection molding tooling can confer numerous advantages to businesses. Here are some critical reasons why it is essential:
1. Efficiency in Production
Quality injection molding tooling can drastically improve manufacturing efficiency. With the right molds, companies can produce parts rapidly with minimal downtime. This efficiency translates to:
- Reduced production costs
- Shorter lead times
- Higher output levels
2. Consistent Quality
One of the most significant benefits of using high-quality tooling in injection molding is maintaining product consistency. The precision involved in creating molds ensures that every part produced meets the same specifications, which is essential for:
- Customer satisfaction
- Minimization of waste
- ACHIEVING regulatory compliance
3. Flexibility and Customization
Modern businesses require the ability to adapt to market demands swiftly. Injection molding tooling allows for:
- Custom mold designs suitable for unique product needs
- Quick changes between different products, enabling companies to pivot as needed
Types of Injection Molding Tooling
When it comes to injection molding tooling, several types are notable, each suited for different applications:
1. Single Cavity Molds
Ideal for small production batches, single cavity molds are straightforward and economical. However, they are less efficient for mass production due to lower output.
2. Multi-Cavity Molds
These molds allow for the production of multiple parts in one cycle, significantly boosting productivity and reducing per-part costs. They are more complex and require higher initial investment but offer great returns in high-volume scenarios.
3. Family Molds
Family molds can produce multiple parts of different shapes in a single cycle. This versatility is valuable for companies looking to produce varied products from the same material without changing molds frequently.
4. Hot Runner and Cold Runner Molds
Hot runner systems are designed to keep the material in a molten state, allowing for quicker cycle times and reduced waste. Cold runner molds, on the other hand, are simpler and cost-effective but might lead to more material waste due to cooling.
Choosing the Right Injection Molding Tooling Partner
Selecting a reliable partner for injection molding tooling is crucial for business success. Here are key considerations when evaluating potential suppliers:
1. Experience and Expertise
Look for partners with a proven track record in the industry. Their experience can provide valuable insights into the complexities of injection molding.
2. Advanced Technology
Ensure that your partner utilizes the latest CAD/CAM technologies and manufacturing techniques. State-of-the-art tools can enhance precision and efficiency.
3. Quality Assurance Processes
Inquire about their quality control measures. Robust testing and verification processes help ensure that the tooling meets all necessary standards.
4. Flexibility
A good tooling partner should be able to adapt to your changing needs, whether scaling up production or customizing designs for specific projects.
Case Study: Success Through Effective Injection Molding Tooling
Let’s explore a case study illustrating the transformative impact of effective injection molding tooling on a metal fabrication company.
Company A, a manufacturer of automotive parts, struggled with inefficiencies in its production line. Parts were produced with varying quality, resulting in reworks and customer complaints. After assessing their tooling processes, they partnered with an experienced tooling supplier who specialized in custom mold solutions.
Through their collaboration, Company A implemented multi-cavity molds and transitioned to a hot runner system. As a result:
- The production rate increased by 60%.
- Quality consistency improved, reducing defects by 40%.
- Production costs were lowered due to reduced material waste and faster cycle times.
This case exemplifies how the right injection molding tooling can enhance operational efficiency and product quality, ultimately leading to higher customer satisfaction.
Future Trends in Injection Molding Tooling
The landscape of injection molding tooling is continually evolving. Some trends to watch include:
1. Automation and Robotics
Incorporating automation in the molding process can drastically improve efficiency and reduce labor costs. Robotics can assist in tasks such as mold handling, assembly, and quality inspection.
2. Sustainable Practices
As businesses increasingly focus on sustainability, innovations are being made to reduce waste and improve energy efficiency in the injection molding process. Environmentally friendly materials and recycling initiatives are gaining traction.
3. Advanced Materials
Developments in materials science are leading to the creation of new thermoplastics and composites that offer enhanced performance characteristics, making them ideal for injection molding applications.
4. Digital Transformation
Utilizing digital technologies, such as IoT and data analytics, can provide real-time feedback and predictive maintenance for injection molding equipment, thereby improving uptime and efficiency.
Conclusion
In summary, injection molding tooling is a cornerstone of modern manufacturing, particularly in the metal fabrication industry. By understanding its nuances, businesses can leverage its advantages to enhance efficiency, ensure quality, and remain competitive in a rapidly changing market. Selecting the right tooling partner and staying informed about emerging trends will pave the way for sustainable growth and innovation.
For more detailed insights and personalized support in injection molding tooling, visit deepmould.net and explore tailored solutions that can meet your specific manufacturing needs.